کاویتاسیون
نویسنده فراپایش2024-12-21T09:19:38-01:00کاویتاسیون یکی از پدیدههای فیزیکی و دینامیکی است که در بسیاری از تجهیزات صنعتی که وظیفه مکش یا دمش را بر عهده دارند رخ میدهد. از آنجا که تأثیرات مخرب کاویتاسیون میتواند منجر به خرابیهای جدی، کاهش کارایی و افزایش هزینههای نگهداری شود، ضروری است جهت تشخیص وجود و جلوگیری از رخداد آن، تدابیر لازم اندیشیده شود. این پدیده در تجهیزاتی که با سیالات کار میکنند، از جمله پمپها، توربینها، پروانهها، کمپرسورها و حتی گیربکسها، مشاهده میشود. در این متن، تلاش میکنیم تا به صورت جامع کاویتاسیون را تعریف کرده، به علل ایجاد آن بپردازیم، علائم وقوع آن را بررسی کنیم، و راهکارهای پیشگیری و مدیریت آن را از دیدگاه پایش وضعیت، به ویژه با استفاده از آنالیز ارتعاش و صدا، ارائه دهیم.
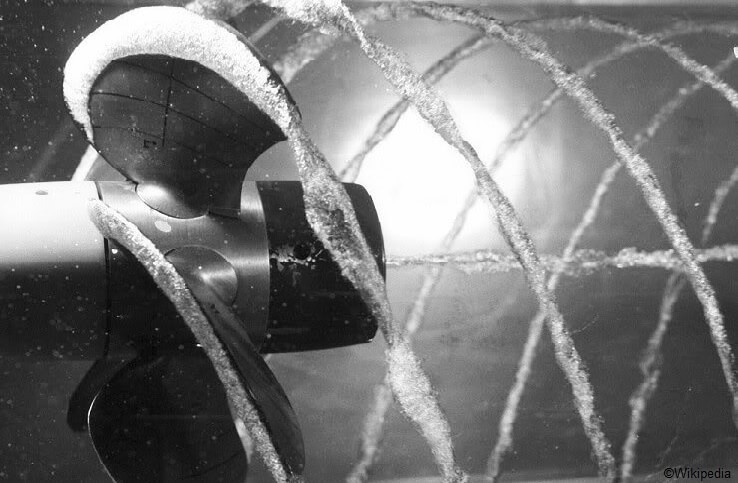
کاویتاسیون چیست؟
کاویتاسیون به فرآیند تشکیل و فروپاشی سریع حبابهای بخار در داخل یک مایع اطلاق میشود. این پدیده زمانی رخ میدهد که فشار مایع در یک ناحیه به کمتر از فشار بخار آن کاهش یابد. این کاهش فشار میتواند ناشی از افزایش سرعت جریان، تغییرات دمایی، یا نوسانات فشاری باشد. پس از تشکیل حبابها، افزایش ناگهانی فشار باعث فروپاشی آنها میشود که این فرآیند میتواند انرژی زیادی آزاد کرده و به سطوحی از تجهیزات که با سیال در ارتباط هستند آسیب وارد کند.
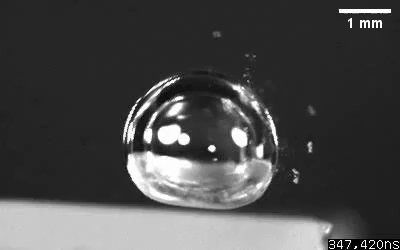
دلایل ایجاد کاویتاسیون
علل بروز این مورد ممکن است متنوع باشد، اما معمولاً به یکی از دلایل زیر مرتبط است:
- تغییرات فشار: کاهش فشار در یک نقطه خاص از سیستم سیالاتی، به ویژه در مناطقی که جریان سرعت بالایی دارد، میتواند باعث ایجاد حبابهای بخار شود.
- طراحی نامناسب تجهیزات: اشکالات طراحی مانند زوایای تیز، جریانهای متلاطم، یا انتخاب نامناسب پروانهها در پمپها و توربینها میتواند منجر به کاویتاسیون شود.
- افزایش دما: افزایش دمای مایع، فشار بخار آن را بالا میبرد و احتمال وقوع کاویتاسیون را افزایش میدهد.
- ارتعاشات و شوکهای مکانیکی: ارتعاشات شدید در تجهیزاتی مانند گیربکسها میتواند شرایط مناسبی برای ایجاد کاویتاسیون فراهم کند.
کاویتاسیون در تجهیزات مختلف
پمپها
پمپها به دلیل ماهیت عملکرد خود بیشترین آسیبپذیری را نسبت به کاویتاسیون دارند. در صورت کاهش فشار در ناحیه ورودی یا افزایش سرعت جریان در پروانه، حبابهای بخار تشکیل شده و سپس در نقاطی با فشار بالاتر فرو میپاشند. این فرآیند معمولاً باعث ایجاد فرسایش پروانه، کاهش راندمان پمپ و حتی خرابی کامل تجهیزات میشود.
در گیربکسها
اگرچه گیربکسها به طور مستقیم با جریان سیالات سروکار ندارند، اما در مواردی که از روغن برای روانکاری استفاده میشود، نوسانات فشار یا ارتعاشات شدید میتواند به ایجاد حبابهای بخار در روغن منجر شود. این نوع کاویتاسیون میتواند باعث سایش سطح دندهها، کاهش کیفیت روغن و در نهایت افزایش احتمال خرابی گیربکس شود.
در توربینها و کمپرسورها
در توربینهای آبی، کاویتاسیون معمولاً در نواحیای که سرعت سیال بالا و فشار پایین است، مانند تیغههای توربین، رخ میدهد. در کمپرسورها، به ویژه نوع سانتریفیوژ، کاویتاسیون میتواند به کاهش راندمان و خرابیهای مکانیکی منجر شود.
در سیستمهای هیدرولیکی و پروانهها
در سیستمهای هیدرولیکی، نوسانات فشار در خطوط انتقال یا طراحی نامناسب شیرها میتواند عامل اصلی کاویتاسیون باشد. در پروانههای کشتیها و زیردریاییها نیز، کاویتاسیون باعث کاهش راندمان و ایجاد نویز میشود که این موضوع برای کاربریهای نظامی بسیار مضر است.
علائم کاویتاسیون
کاویتاسیون علائمی دارد که در صورت آگاهی از آنها میتوان به سرعت این پدیده را شناسایی و مدیریت کرد. این علائم شامل:
ایجاد نویز و صداهای غیرعادی: صدای کاویتاسیون معمولاً شبیه ضربات یا ترکیدن حبابها است و به عنوان یکی از شاخصهای اولیه در پایش وضعیت استفاده میشود.
ارتعاشات بالا: کاویتاسیون معمولاً باعث افزایش ارتعاشات در تجهیزات میشود، به ویژه در نقاطی که حبابها فرو میپاشند.
کاهش راندمان: کاهش فشار یا سرعت جریان در سیستم میتواند نشاندهنده تأثیرات کاویتاسیون باشد.
آسیبهای سطحی: نقاط فرسوده یا خوردگی روی تیغهها، پروانهها یا سطوح داخلی تجهیزات از دیگر نشانههای کاویتاسیون است.
روشهای پیشگیری
برای پیشگیری از وقوع کاویتاسیون و کاهش اثرات مخرب آن، باید از رویکردهای جامع و متنوعی بهره برد. اولین قدم در این مسیر، طراحی بهینه تجهیزات است. استفاده از طراحیهایی که جریان مایع را یکنواخت و بدون تلاطم هدایت میکنند، میتواند تا حد زیادی از وقوع کاویتاسیون جلوگیری کند. به عنوان مثال، انتخاب پروانههایی با زوایای مناسب، کاهش وجود نقاط تیز و جریانهای متلاطم، و بهینهسازی مسیرهای سیال در سیستم، فشارهای ناگهانی را کنترل کرده و از تشکیل حبابهای بخار جلوگیری میکند.
نقش مدیریت شرایط عملیاتی در پیشگیری از کاویتاسیون
مدیریت شرایط عملیاتی نیز نقش مهمی در پیشگیری از کاویتاسیون ایفا میکند. کنترل سرعت جریان مایعات، به خصوص در نقاط بحرانی سیستم، باعث میشود تا فشار در محدودهای ایمن باقی بماند و احتمال کاهش فشار تا زیر فشار بخار به حداقل برسد. از سوی دیگر، نظارت دقیق بر دمای سیال اهمیت زیادی دارد. افزایش دما میتواند فشار بخار سیال را افزایش دهد و احتمال تشکیل حبابهای بخار را بالا ببرد؛ بنابراین، پایش دما و استفاده از تجهیزات خنککننده یا گرمایش مناسب برای حفظ دمای سیال در محدوده استاندارد، یکی از اقدامات کلیدی است.
استفاده از مواد مقاوم در برابر فرسایش و سایش نیز یکی از دیگر راهکارهای مؤثر در این زمینه است. تجهیزاتی که در معرض شرایط سخت عملیاتی قرار دارند، مانند پروانهها، تیغهها یا دیوارههای داخلی سیستم، باید از موادی ساخته شوند که مقاومت کافی در برابر فرسایش ناشی از فروپاشی حبابها داشته باشند. این کار نه تنها طول عمر تجهیزات را افزایش میدهد، بلکه هزینههای تعمیر و نگهداری را نیز کاهش میدهد.
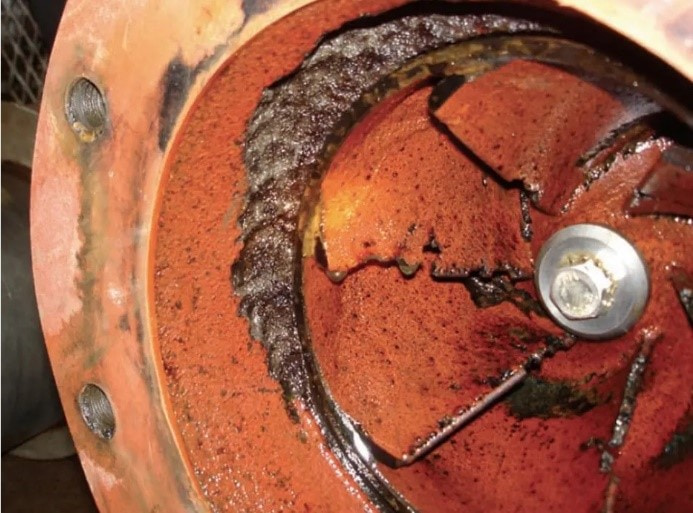
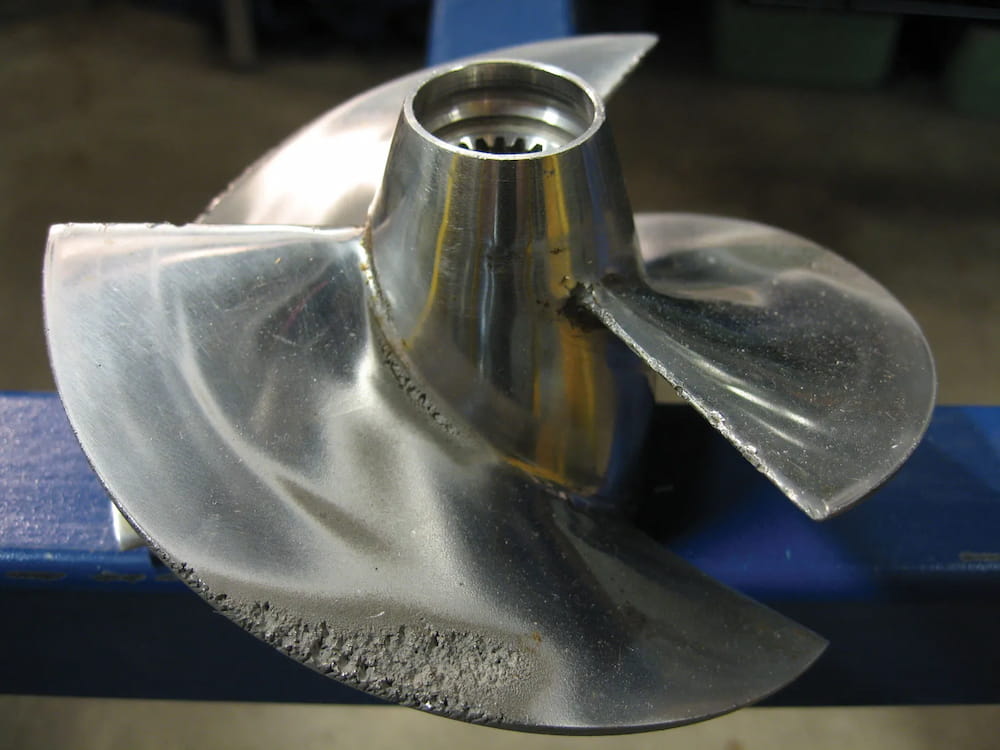
این مطلب را از دست ندهید: واشبورد در بیرینگها (Washboard)
پایش وضعیت مؤثرترین ابزار شناسایی و پیشگیری از کاویتاسیون
یکی از مؤثرترین ابزارها در شناسایی و پیشگیری از کاویتاسیون، بهرهگیری از تکنولوژیهای پایش وضعیت است. آنالیز ارتعاش یکی از تکنیکهای اصلی در این حوزه است که با پایش ارتعاشات ایجاد شده در تجهیزات، نقاطی که تحت تأثیر کاویتاسیون قرار گرفتهاند را شناسایی میکند. این روش به ویژه در پمپها و توربینها کاربرد دارد و میتواند اطلاعات دقیقی درباره شدت و محل وقوع پدیده ارائه دهد. علاوه بر آن، آنالیز صدا یا روشهای اولتراسونیک نیز ابزار دیگری است که امکان شناسایی صداهای غیرمعمول ناشی از ترکیدن حبابهای کاویتاسیون را در مراحل اولیه فراهم میکند. این روش، به دلیل دقت بالا و قابلیت شناسایی مشکلات قبل از وقوع خرابیهای جدی، به یکی از روشهای پرکاربرد در تشخیص کاویتاسیون تبدیل شده است.
در نهایت، برای پیشگیری از کاویتاسیون، ترکیبی از رویکردهای طراحی بهینه، مدیریت عملیاتی و استفاده از فناوریهای پیشرفته پایش وضعیت ضروری است. این راهکارها نه تنها مانع وقوع این پدیده میشوند، بلکه عملکرد تجهیزات را بهبود داده و هزینههای ناشی از خرابیهای احتمالی را کاهش میدهند.
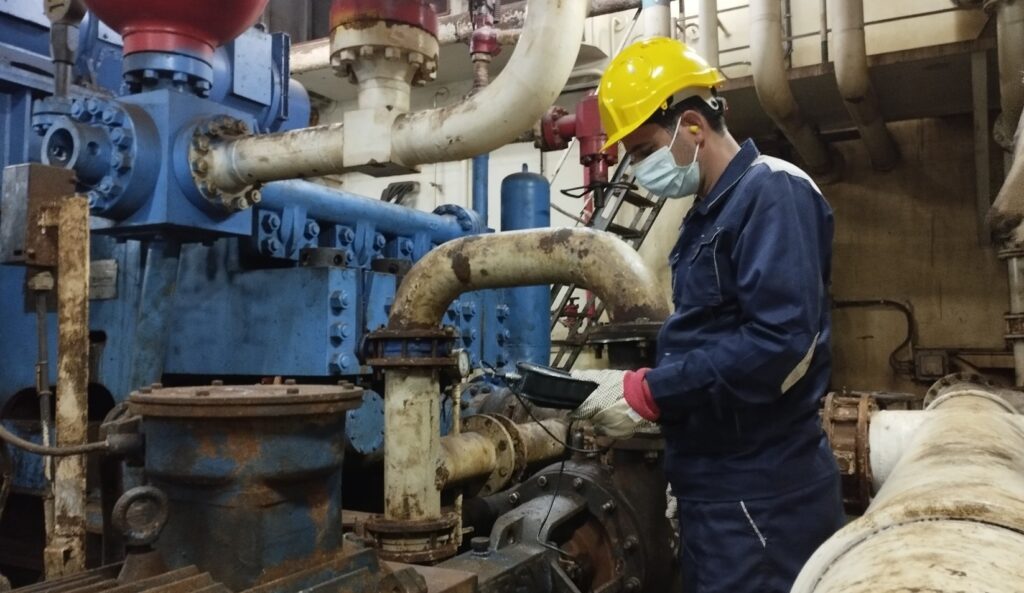
نتیجهگیری
این پدیده پیچیده و زیانآور که در بسیاری از تجهیزات صنعتی، به ویژه پمپها، گیربکسها و توربینها رخ میدهد. شناسایی به موقع علائم کاویتاسیون و استفاده از تکنیکهای پیشرفته پایش وضعیت میتواند به کاهش تأثیرات مخرب این پدیده کمک کند. با بهرهگیری از روشهای طراحی بهینه، مدیریت شرایط عملیاتی و استفاده از تکنیکهای آنالیز ارتعاش و صدا، میتوان از خرابی تجهیزات جلوگیری کرده و عمر مفید آنها را افزایش داد. جهت کسب اطلاعات و جزئیات بیشتر در زمینه آنالیز ارتعاشات و تشخیص خرابی تجهیزات دوار به روش آنالیز ارتعاشات با ما در تماس باشید.
“اشتراکگذاری مطالب با ذکر منبع آزاد است.”
دیدگاهتان را بنویسید